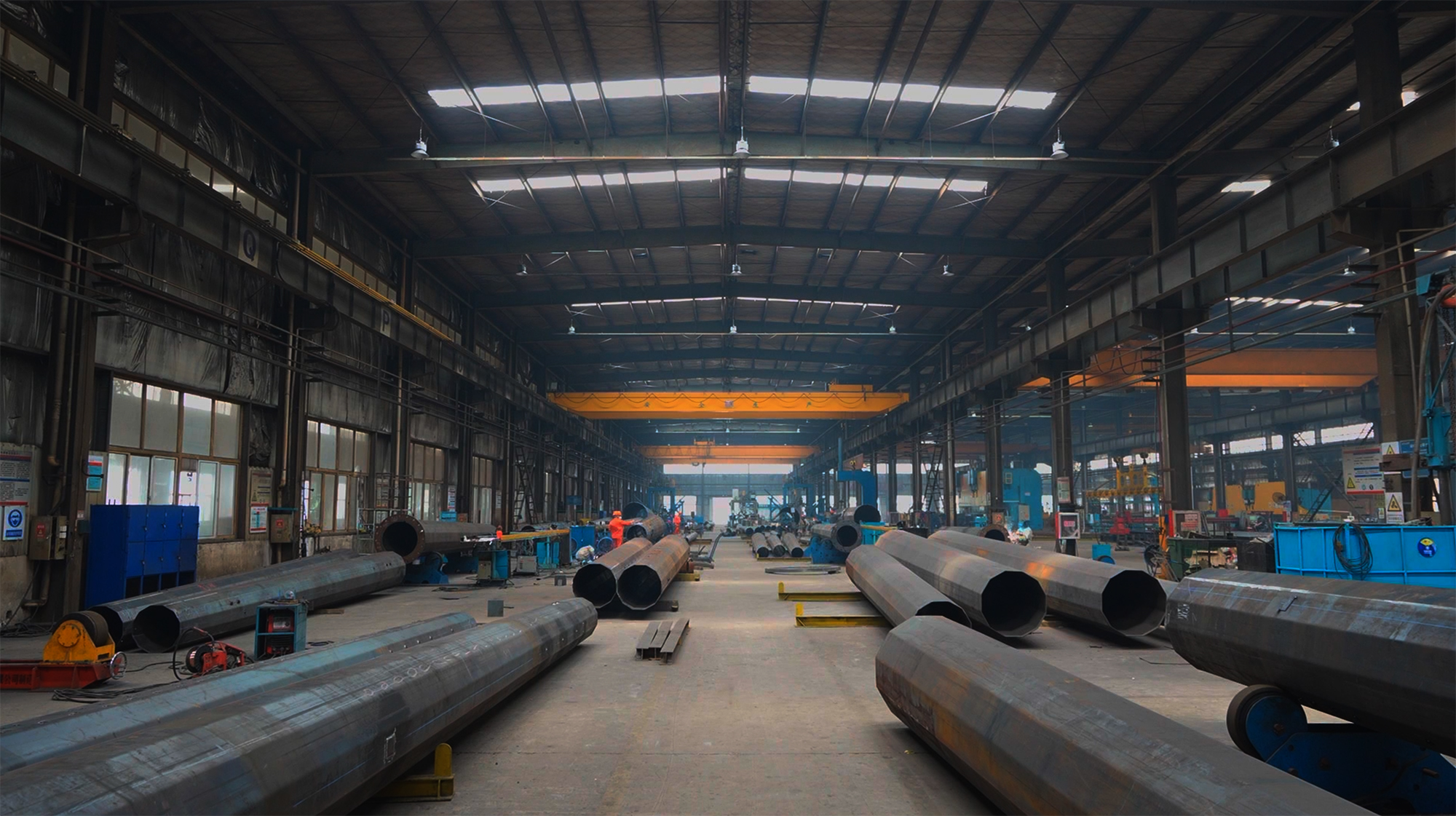
Our Process
At IUP, our commitment to clients through responsive support and diligent operations is evident at every stage of our process. Here is how we help your project succeed.
Drawings & Steel Procurement
After the purchase order or contract is executed, the initial step at IUP is to prepare the Approval Drawings. These drawings serve as a guide for the structural aspects of poles, illustrating crucial features, such as attachment points, through-holes and welded nuts. While structural approval is our responsibility, the client’s approval is sought to ensure the design precisely aligns with their requirements.
At the commencement of the drawing phase, the design loads for each pole type are locked in. This is a critical step, as it allows us to order the correct steel thickness for each pole. Any subsequent line design changes after this point may warrant a redesign to accommodate increased pole loads. We immediately advise our clients of any impacts to the delivery schedule as a result of such changes.
Once approved, the drawings are then translated into Chinese for the manufacturing team using DWG files.
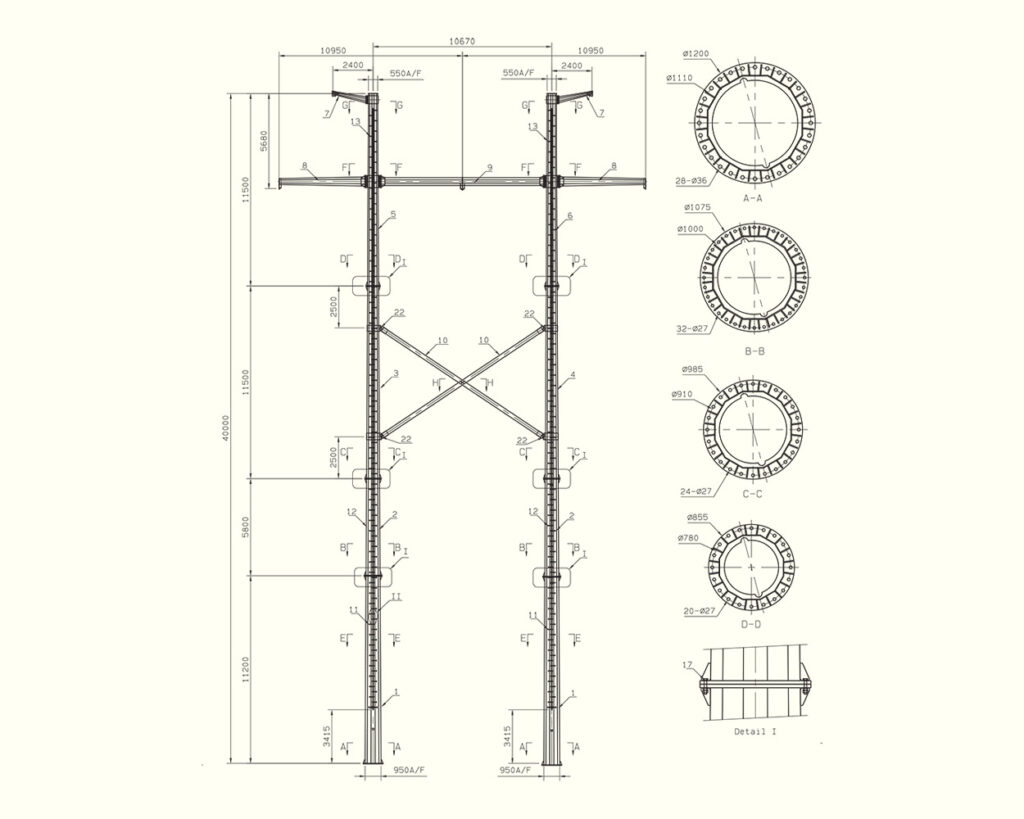
De-coiling & Trapezoid Cutting
With the project officially scheduled for production and the drawings released, the manufacturing process begins with de-coiling, straightening and cutting sheet steel into the required section lengths for pole construction. Each section of a pole is treated as a separate item during this phase, with its own set of drawings and QA (Quality Assurance) paperwork.
Following the cutting phase, the sheet and plate are taken to a CNC plasma cutter to shape them into trapezoids. This step is particularly vital for tapered poles, ensuring that the finished section has the correct top and base diameters (a characteristic predetermined during the design stage). The plasma cutter also marks each end of the trapezoid with equally spaced bend lines, which play a crucial role in the subsequent manufacturing stages.
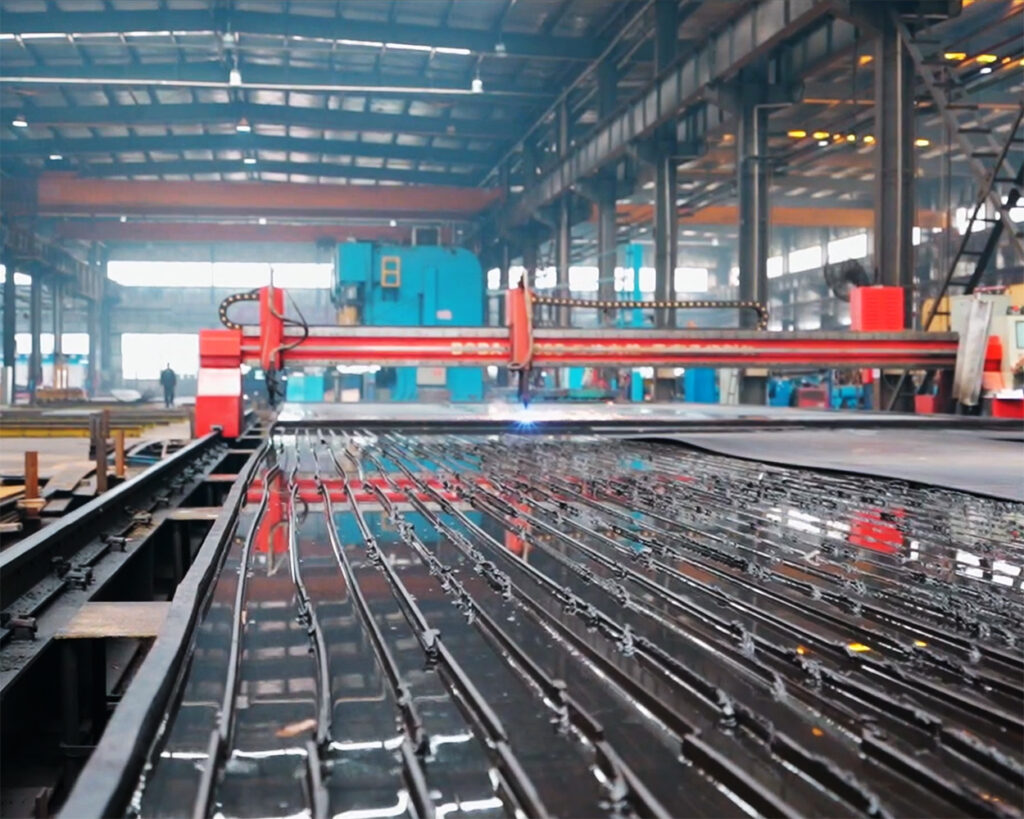
Trapezoid Bending, Seam Welding & Fabrication
The trapezoids move to a brake press, where they undergo bending along the marked lines, ultimately forming the desired section shape. From here, the formed sections are transported to a seam welder, where the open side is welded closed, utilising submerged arc welding (sub-arc or SAW). This process ensures about 80% penetration weld, with specific attention given to achieving a 100% penetration weld in the slip area of the pole sections, where needed.
The fabrication stage is where all other components essential for pole construction are added. This includes items such as:
- Top caps
- Base plates
- Earth points
- Brackets (for climbing systems)
- Through-holes
- Through-tubes
- Galvanising hanging holes
- Drainage holes
During this phase, any required holes are drilled, and the pole sections begin taking their final shape.
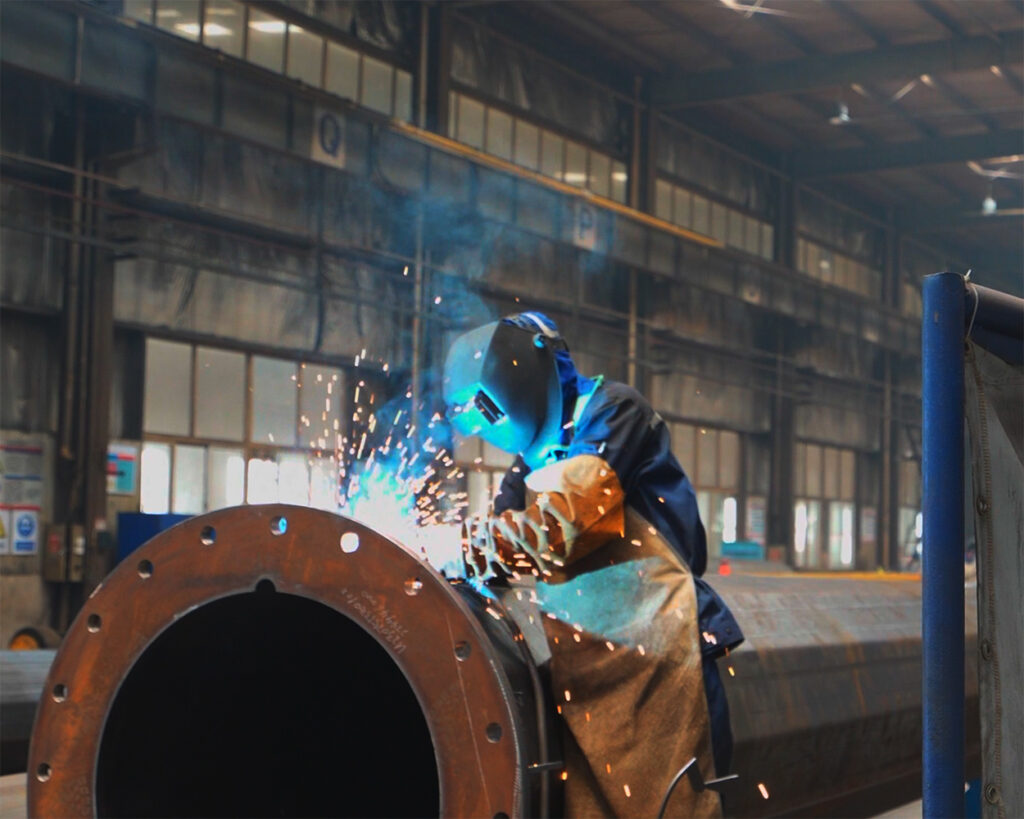
Hot-Dip Galvanising & Painting
After fabrication, the pole sections undergo hot-dip galvanising, adhering to AS/NZS 4680. The process starts with lowering the sections into the acid tank for ‘pickling’, to clean and slightly etch the surface. Subsequent immersion into a rinse tank follows to remove most of the acid.
The sections are then lowered into the zinc tank, using a combination of metals (but predominantly zinc). The metallurgical reaction between zinc and steel forms a zinc-iron alloy, providing superior corrosion protection. The change in metallurgy results in a higher melting point; approximately 200°C higher than that of pure zinc. The sections are rigorously checked to ensure compliance with the average and minimum thickness requirements.
Poles may undergo painting for one of two reasons: additional corrosion protection at the ground line of an in-ground pole or to alter the colour of the pole’s finish. For ground line protection, a coating of 200 microns dry film thickness (DFT) of Interseal 670HS two-pack epoxy from International® is applied.
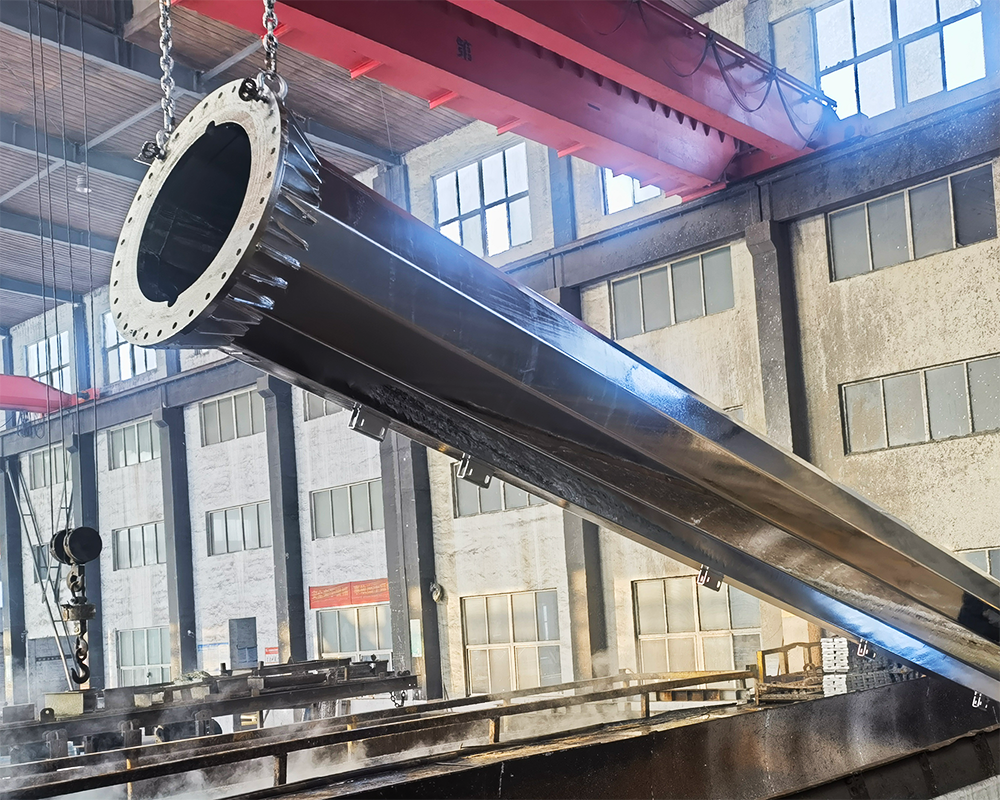
Packing, Freight & Delivery
Following the thorough post-galvanising checks, pole sections are bundled for transportation. The goal is to maximise container space. Where possible, sections for the same pole are packed together, and sections are commonly nested together, where smaller upper sections may be placed inside larger base sections. Timber gluts and a combination of polypropylene strapping and wide ratchet straps secure these nested sections for their journey, anticipating the likelihood of long-distance travel by road after reaching the Australian port.
Packed containers then head to the nearest seaport and are transported to the destination port by container ship. Tracking options are available for containers after departure from the port of origin. And direct shipping options are available for Sydney and Melbourne, while other Australian ports often involve transhipment in Singapore or Port Klang (Malaysia).
Upon arrival at the destination port, containers are de-stuffed, and the complete bundles are typically loaded onto semi-trailers. The loaded bundles are then transported to the agreed delivery location, where unloading is usually handled by the contractor on-site. (While IUP can arrange unloading, we have discovered it can be more practical for the on-site contractor to handle this stage using their own equipment.)
Detailed packing lists provided at this stage aid in determining the required rigging and machinery for unloading on-site. For unloading, the recommendation is to use fibre or soft slings, as steel chains are not recommended (as they can potentially damage the zinc surface).
While IUP is committed to ensuring complete poles only in each container, occasionally, sections of the same pole may be packed in different containers. This is a factor that needs consideration during the quoting process.
IUP maintains open communication with you throughout every step of our process, ensuring your product precisely suits your requirements and is delivered in a diligent, timely manner.
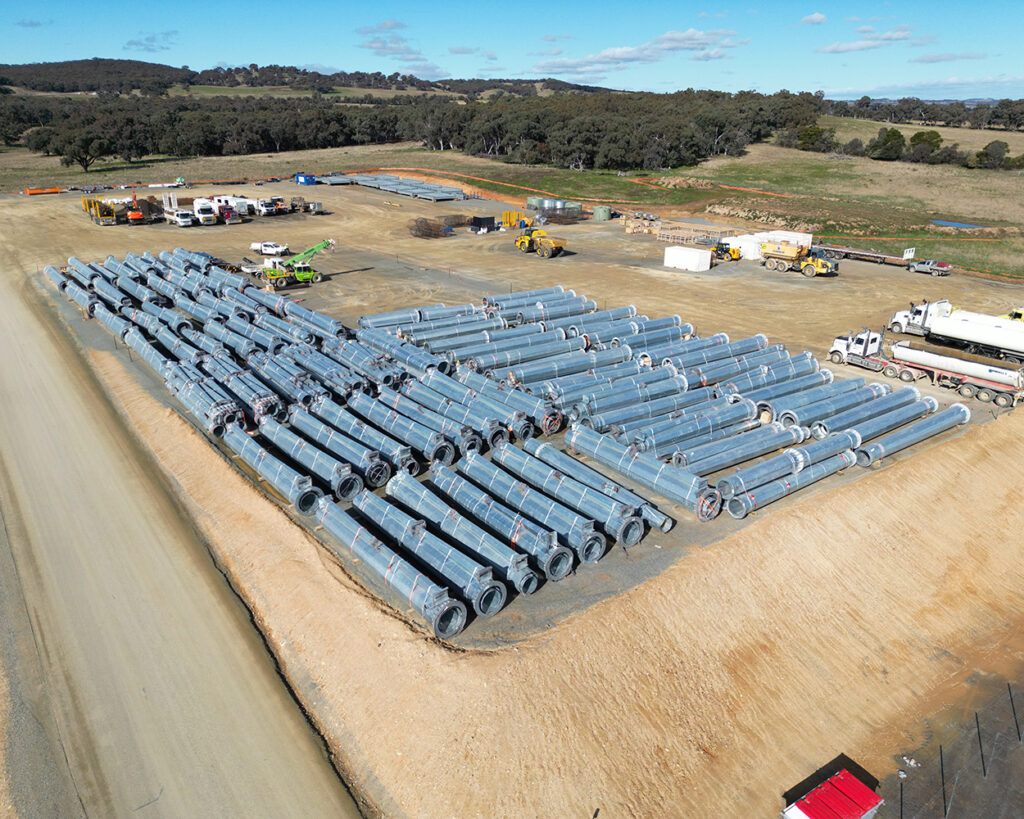